¿Cómo utilizar la fundición de espuma perdida para producir fundiciones de acero de alta calidad?
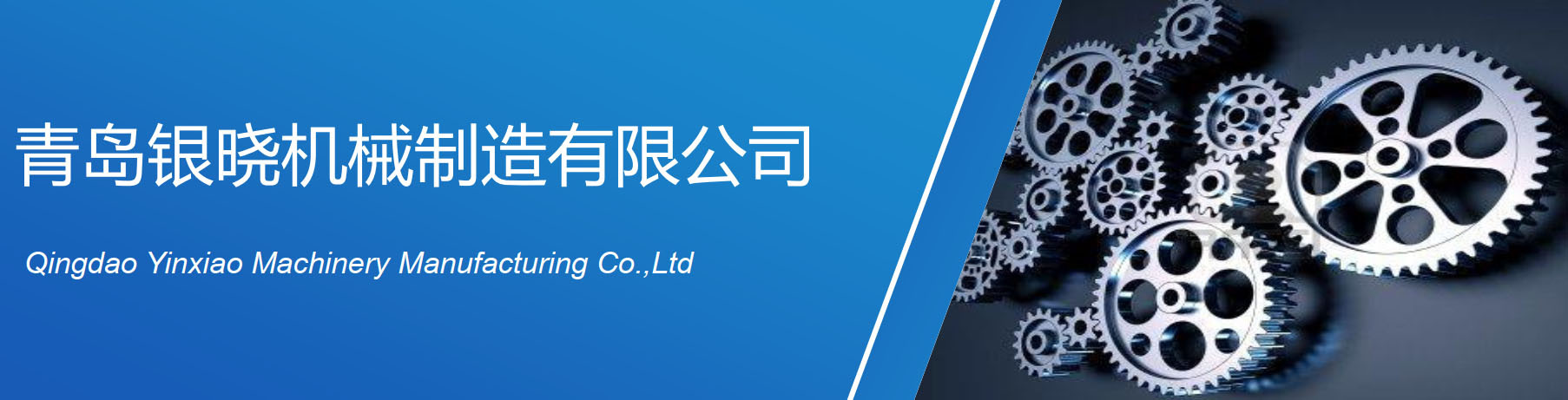
¿Cómo utilizar la fundición de espuma perdida para producir fundiciones de acero de alta calidad?
La fundición de espuma perdida tiene las ventajas de una operación de proceso simple, bajo costo de consumo de material, superficie lisa, alta precisión dimensional y menos contaminación ambiental. Se ha promovido y aplicado vigorosamente a finales de la década de 1990 en mi país, especialmente en fundiciones de hierro. Ha logrado un buen éxito. Experiencia, como la aplicación de piezas de hierro gris en la caja y la carcasa. Sin embargo, no hay mucha experiencia exitosa en el uso de espuma perdida en fundiciones de acero, especialmente en acero con bajo contenido de carbono. La razón principal es que las piezas fundidas de espuma perdida son propensas a defectos de desviación de la composición química que aumentan el carbono.
¿Cómo optimizar y controlar los procesos clave en el sistema de producción para producir fundiciones de acero calificadas con menores costos?
Evitar el aumento de carbono
Las piezas fundidas de acero de espuma perdidas son propensas a defectos de carburación. La razón principal de los defectos por aumento de carbono de las piezas de acero es que el material de espuma contiene carbono y la espuma se quema y descompone el carbono libre durante el vertido, y el carbono invade el acero fundido.
Después de la experimentación, se encuentra que el aumento de carbono tiene una cierta regularidad, es decir, la superficie de la fundición aumenta el carbono, pero el núcleo apenas aumenta el carbono; no hay aumento de carbono cerca de la puerta interior, y cuanto más lejos de la puerta interior, más grave es el aumento de carbono. Tome las siguientes medidas correspondientes para hacer que la composición de fundición esté básicamente dentro del rango de requisitos del proceso.
(1) La clave es elegir materiales de espuma con bajo contenido de carbono. En la actualidad, existen tres materiales principales para la fundición de espuma perdida: EPS, STMMA y EPSMMA, y su contenido de carbono disminuye secuencialmente. Entre ellos, el EPS se caracteriza por un gran contenido de carbono, pero su generación de gas es pequeña, no es fácil de pulverizar durante el vertido, su precio es económico y se utiliza ampliamente en fundiciones de hierro y acero con bajos requisitos.
El EPSMMA se caracteriza por un bajo contenido de carbono, pero una gran salida de gas, que es fácil de provocar una contrapulverización, y el material es caro, y generalmente se usa más en acero de baja aleación. STMMA tiene en cuenta las ventajas de ambos, tiene las ventajas de menos gas y bajo contenido de carbono, y es el material de elección para la producción de fundiciones de acero en espuma perdida.
(2) Aprovechando la característica de que cuanto más lejos de la puerta interior, más grave es el aumento de carbono, la contrahuella se coloca en la distancia más lejana de la puerta interior o en el punto más alto de la fundición, de modo que el acero fundido con un serio aumento de carbono, la contaminación que ingresa al molde entra primero en el molde. En la boca, el elevador también juega un papel de recolección de escoria y gas. El uso de este proceso para piezas de acero puede controlar el contenido total de carbono de las piezas de fundición dentro de los requisitos del proceso.
(3) La densidad del patrón perdido es muy importante. Siempre que la superficie sea lisa y la densidad sea baja, se pueden obtener los beneficios de un aumento bajo en carbono y una menor generación de gas.
Prevenir el spray para la espalda
El spray para la espalda es un fenómeno común en la fundición de espuma perdida. Si el aerosol para la espalda es grave, puede poner en peligro la seguridad personal de la persona que rueda. Hay que prestarle atención. Para reducir el fenómeno de la pulverización, se pueden tomar las siguientes medidas.
(1) La densidad del modelo de espuma debe ser pequeña. Bajo la premisa de garantizar la calidad de la superficie de la espuma y la resistencia del modelo, cuanto más ligera debe ser la espuma, mejor, para reducir la cantidad de gas durante el vertido.
(2) El modelo de espuma debe secarse antes de aplicar la pintura. Se debe tomar una muestra de cada lote de modelos de espuma de las piezas fundidas de acero para ver el cambio de peso durante el proceso de secado, y se debe hacer el gráfico de curva de cambio de peso de horneado. Solo cuando el peso ya no cambie. Pintar.
(3) El sistema de vertido, especialmente el bebedero y el canal transversal, no debe recubrirse con pintura, de modo que el gas generado durante el vertido se pueda extraer rápida y completamente, y no se aplique recubrimiento, lo que ahorra el consumo de pintura.
(4) Cubra una placa deflectora en la parte superior de la copa del bebedero, que puede bloquear el acero fundido que se vuelve a rociar, de modo que no pueda salpicar y poner en peligro a los operadores en el lugar.
El papel principal de los recubrimientos en la espuma perdida.
(1) Evite el contacto directo entre el acero fundido y la arena para garantizar la calidad de la superficie de la pieza fundida;
(2) Mejorar la resistencia de la espuma para que no se deforme durante la manipulación;
(3) El gas generado durante el vertido se agota y se extrae a través del revestimiento.
Cepillado y secado de pintura
(l) Es mejor no terminar la pintura de una sola vez. Debido a que la pintura es muy espesa y fácil de agrietar, debe aplicarse de dos a tres capas. El espesor total del revestimiento debe controlarse en aproximadamente 1 mm.
El principio de control del espesor del revestimiento es que el revestimiento debe ser lo más fino posible con la premisa de que la pieza fundida no se adhiera a la arena, de modo que el gas pueda descargarse a través del revestimiento lo antes posible.
(2) Cada capa de pintura debe secarse antes de la siguiente ronda de pintura o escultura. Si el revestimiento no está completamente seco, el acero fundido generará una gran cantidad de gas cuando se encuentre con la humedad durante el vertido, lo que provocará una salpicadura. Además, el recubrimiento si no está completamente seco, la pintura tiene poca permeabilidad al aire y el gas no se puede descargar a tiempo. Es probable que las piezas fundidas de acero produzcan poros y agujeros de escoria en las piezas fundidas.
Prevenir el colapso
Cuando hay muchas piezas fundidas en serie en una caja, debido a que cada modelo se vaporiza al mismo tiempo, el vacío no es suficiente y es fácil provocar el colapso de la caja. Para evitar el colapso de la caja, preste atención a:
(1) Mantenga un vacío suficiente y estable en el matraz.
(2) Controle la temperatura de vertido y, al mismo tiempo, la velocidad de vertido debe ser lo más consistente posible con la velocidad de gasificación del modelo para evitar que la barrera fría se vierta demasiado lentamente y provoque el colapso de la caja.
El más tabú de la operación de vertido de fundición de espuma perdida es el vertido intermitente, que fácilmente causa defectos de barrera contra el frío en las piezas fundidas, es decir, la temperatura del metal fundido vertido primero disminuye, lo que resulta en una barrera fría entre el metal fundido vertido posteriormente.
Además, el sistema de vertido de fundición de espuma perdida utiliza principalmente un sistema de vertido cerrado para mantener la estabilidad de vertido. En este sentido, la forma de la taza de vertido está estrechamente relacionada con si la operación de vertido es estable. Durante el vertido, el nivel de líquido en la taza de vertido debe mantenerse estable para que la cabeza de presión dinámica de vertido sea estable.
La presión negativa es una medida necesaria para la fundición de espuma perdida de aleación negra. El papel de la presión negativa es una medida importante para aumentar la resistencia y rigidez del molde de arena, y también es la principal medida para eliminar los productos de gasificación del modelo. La magnitud y el tiempo de retención de la presión negativa están relacionados con el material de fundición, la estructura del grupo de modelos y el revestimiento.
Para revestimientos con buena permeabilidad al aire y un espesor de revestimiento inferior a 1 mm, la presión negativa en las piezas de fundición de hierro es generalmente de 0,04 ± 0,06 MPa, y el límite superior se toma para las piezas de acero. Para las piezas de fundición de aluminio, la presión negativa generalmente se controla a 0.02 ± 0.03MPa.
El tiempo de retención de la presión negativa depende de la estructura de los grupos de modelos. En el caso de un gran número de grupos de modelos en cada caja, el tiempo de retención de la presión negativa se puede extender adecuadamente. Generalmente, la presión negativa puede eliminarse cuando la costra solidificada en la superficie de la pieza fundida alcanza un cierto espesor. Para recubrimientos más gruesos y poca permeabilidad al aire, la presión negativa y el tiempo de retención se pueden aumentar de manera apropiada.